Not just new products. Introducing Manufacturing Innovation
Mention innovation and most people think about New Product Development (NPD). But there’s more to it than that. Innovating how you make your products can be powerful and with the emerging possibilities of new technology, the potential is huge. Find out more about the world of Manufacturing Innovation.
What this article is about
You don’t hear the phrase “Manufacturing Innovation” very often. Certainly not as much as Product or Process Innovation. But it’s a field that has a proven record of delivering value. It’s innovation that impacts how manufacturing is organised and carried out in its wider sense. It can include elements of Process Innovation, but it’s more than that. New process technologies can be enablers of Manufacturing Innovation.
Manufacturing Innovation doesn’t necessarily deliver new products, but it can make products more quickly, cheaply or with higher quality. To give you an example, the Industrial Revolution in the late 18th and early 19th centuries was powered by Manufacturing Innovation.
Let’s have a closer look at that and other historical examples
Proven successes – examples of Manufacturing Innovation
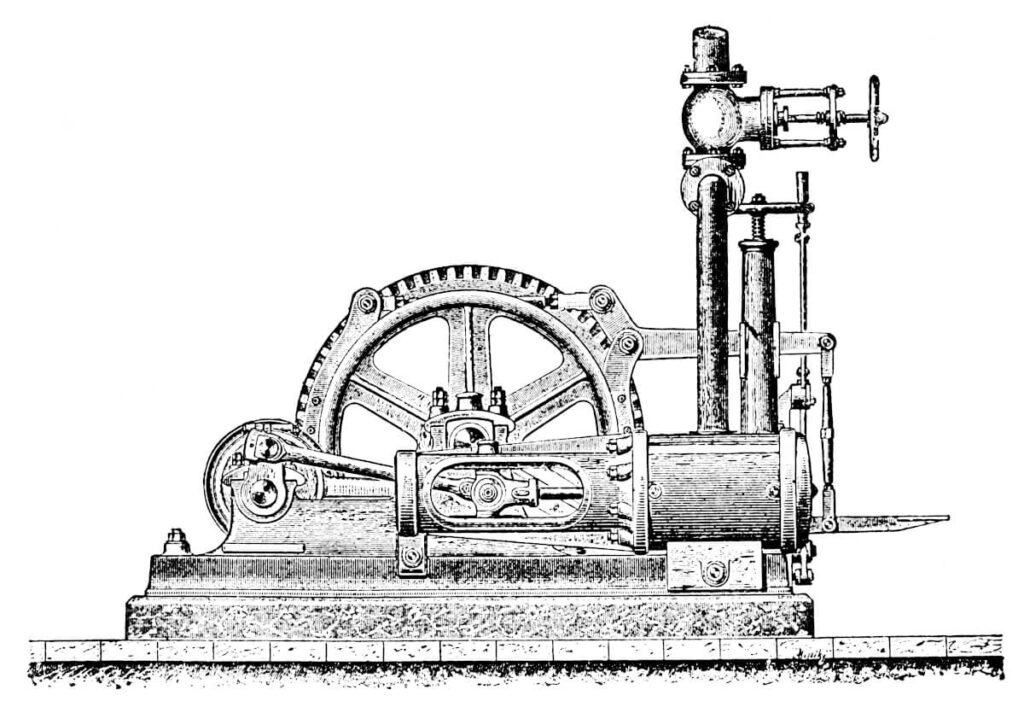
The Industrial Revolution
The Industrial Revolution in Europe (1760-1840) moved production from artisanal, hand-made methods to factory-based industrial methods.
This resulted in large increases of output and profound social change.
This period of extended manufacturing innovation was facilitated by technological developments in various fields including:
Efficient industrial steam engines for powering factories and transportation.
Mechanised cotton spinning and textile weaving.
Industrialised iron making using coke instead of charcoal with mechanical ventilation of the blast furnaces.
New gas lighting technology which replaced tallow candles and allowed longer working hours in factories.
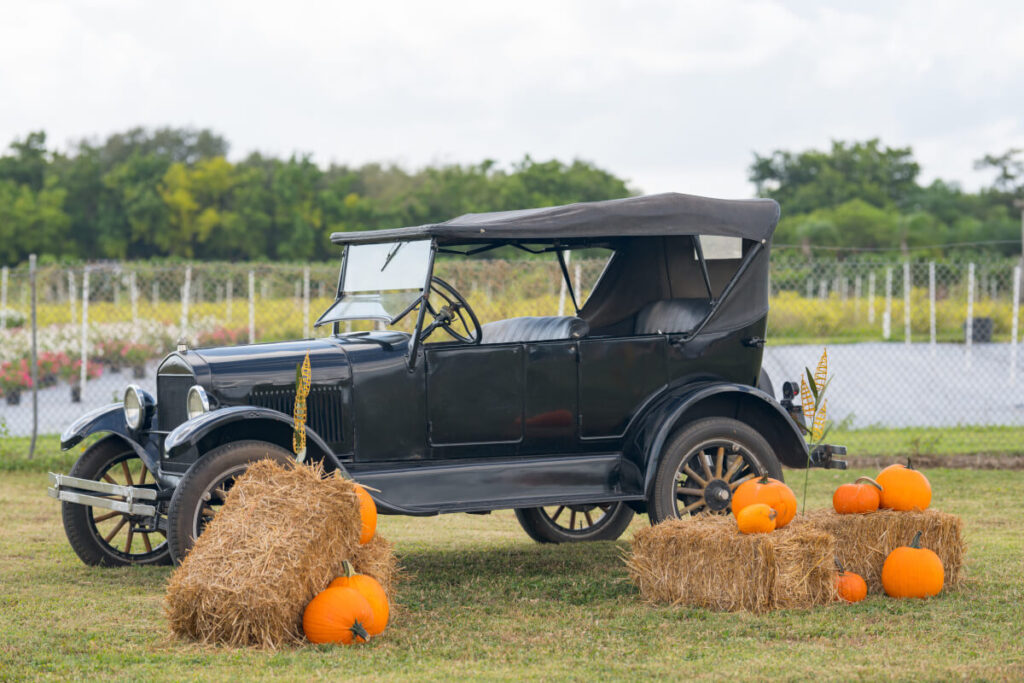
Assembly Line Production
Assembly Line Production was introduced by Eli Whitney in the USA and was further developed by the Ford Motor Company in 1913.
By continuously moving the cars past individual workstations, Henry Ford was able to reduce the production time for a single car from over 12 hours to 93 minutes.
This manufacturing innovation was not necessarily enabled by technology, even if conveying systems were needed to physically move the product along the assembly line. The main change here was in working practices. Workers no longer carried out all the tasks required to build a car. They specialised in one task, which they repeated continuously.
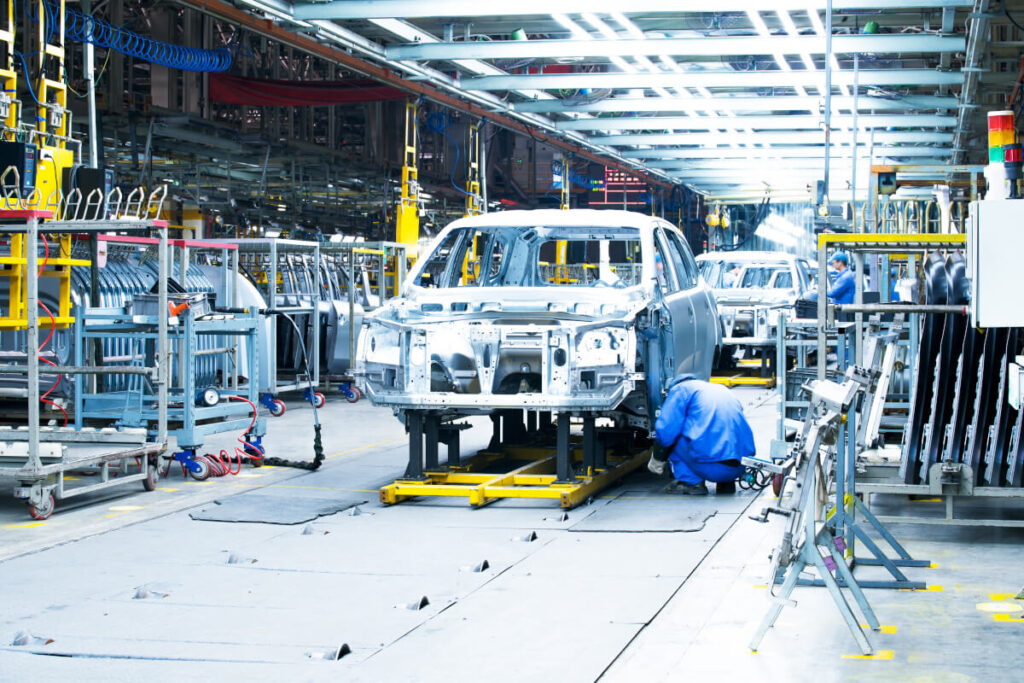
Japanese Car Manufacturing
The Japanese car industry gained market share around the world in the 1970s. This was all the more surprising since, post world war two, Japanese cars were seen as being notoriously bad quality.
They were particularly successful in the US market where Japanese cars were cheaper to buy, more economic to run and more reliable than their US counterparts. So how did they transform the fortunes of their industry? A main contributor to this success story was a novel and decades-long focus on Quality Management.
After the second world war, Japan needed to re-build its industrial capability and Japanese car manufacturers actively searched for best practices from around the world. They integrated elements of “Scientific Management Theory” and Statistical Process Control with their own culture of teamworking and collective problem solving. This unique approach progressively developed into techniques such as Kaizen, Kanban and Just in time.
This new manufacturing approach and underlying philosophy delivered higher productivity and fewer quality defects. It meant cheaper, better cars hit the American markets. Product Innovation played a part too. Japanese manufacturers had developed smaller, more efficient, less polluting motors than their American competitors which meant Japanese cars were also cheaper and cleaner to run.
But make no mistake, the real driver behind the growth of the Japanese car industry was their innovative manufacturing approach, an approach that has since been adopted by all kinds of industries around the world.
Not all Manufacturing Innovation leads to widespread industry changes. A more modest example is Late Differentiation.
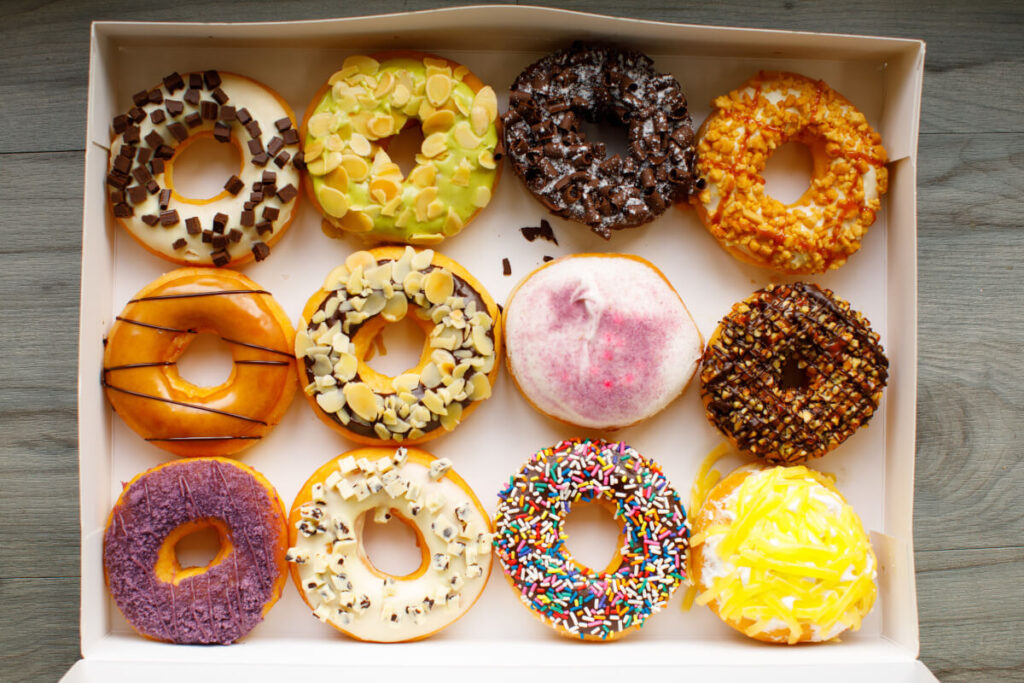
Late Differentiation
Late Differentiation is a manufacturing concept that delivers variety to consumers while minimising manufacturing complexity. The approach consists of making a common “base” that is shared across several product lines and adding “customising” ingredients as late as possible at the end of manufacturing.
For example, a factory using Late Differentiation to produce a range of fruit yogurts makes one plain yogurt “base” that is used in all variants. The final fruit preparation, flavours and other minor ingredients are added as late in the process as possible, just before filling into pots.
Manufacturing this way, as opposed to adding all ingredients at the start of the process allows for economies of scale, reduced cleaning times and reduced waste during product changeover. The technology needed for late differentiation is usually not new. The innovative element is the way product and process design are integrated to make late differentiation possible.
What’s next? Industry 4.0?
Right now there’s a lot of buzz about Industry 4.0, or “the 4th Industrial Revolution”. As a result, articles on Manufacturing Innovation trends are mostly about how digitalisation will revolutionise factories.
However, it’s all still at an early stage.
Some technologies like immersive technology, additive manufacture and wearable devices still need to show their real applicability in food production. For example, 3D printing is still unable to make products at the volumes required for large scale food manufacture.
Other technologies seem further advanced and are starting to be applied to the agri-food sector.
Automation and robotics have been used for a while in many industries and recent developments are making their use cheaper and more flexible.
Big data analysis, AI and the use of digital twins are gaining more traction in food manufacturing. This IFT article from 2021 contains some examples and a good overview of the topic. See-d is a French company that uses data science to help companies perform better. They have proven use cases for the application of data science in agri-food production.
Summing it up…
Manufacturing is an area where innovation can yield game-changing results. Compared to Product Innovation, it’s advantage is that it can potentially affect all your products, not just a few of them.
The current trends in Manufacturing Innovation are related to Industry 4.0 and rely on digitalisation. While it’s worth staying informed of emerging Industry 4.0 technologies, keep in mind that not everything is proven (yet). If you’re serious about investigating this area, my advice is find a reliable 3rd party expert to guide you through what it can and cannot do for you.
In parallel, remember that Manufacturing Innovation is not limited to Industry 4.0. Perhaps a new process technology can unlock a whole new way of manufacturing your products. Maybe changing the organisation of your manufacturing teams can boost productivity.
Whatever your approach, the first thing to get right is to be clear about what you want to achieve by changing how you make your products.
The potential of Manufacturing Innovation is huge, and who knows, perhaps your innovation will result in an industry-wide revolution one day too.
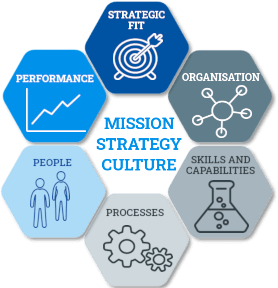